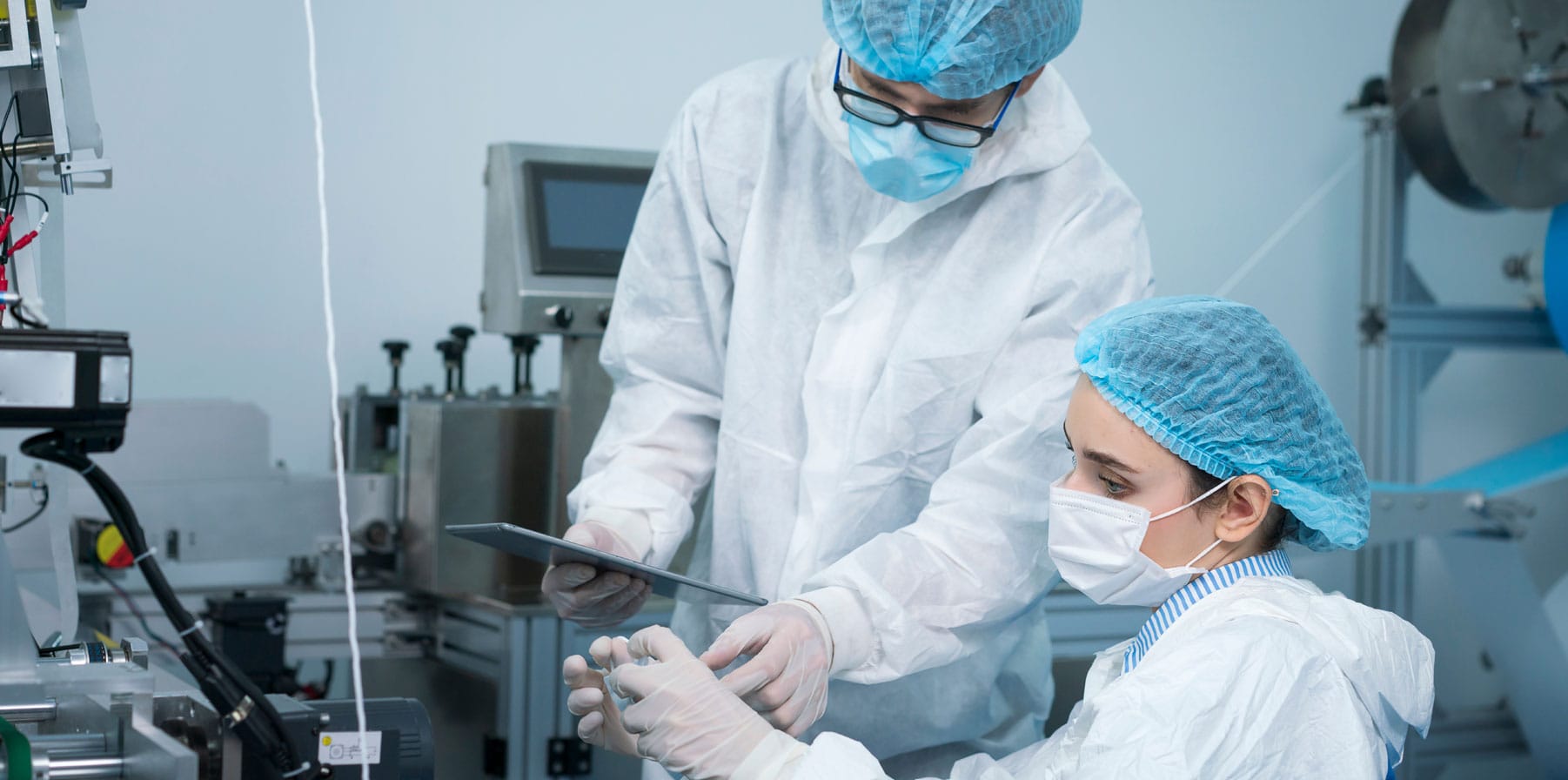
Engineering-focused Scalable Global Development and Manufacturing
Phillips Medisize combines the customer-first culture with new product introduction teams and global manufacturing with scale and deep experience of one of the largest contract development and manufacturing organizations (CDMOs). In fact, we are one of the few medical CDMOs capable of small volumes to high volumes in the hundreds of millions for our pharmaceutical, medical device and in vitro diagnostic customers.
Across three continents, the Phillips Medisize team of highly skilled engineers improves efficiencies and lowers production costs, while leveraging our Safety, Quality, Delivery and Cost (SQDC) operating system and one Quality Management System (QMS).
Our advanced manufacturing capabilities include:
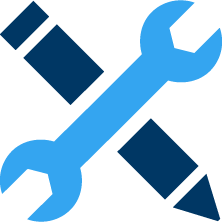
- Technical components’ specifications for development of pen and cartridge assembly lines
- Purpose-built clean room and controlled manufacturing sites
- Complex, highly sophisticated injection molding, including reel-to- reel insert molding
- Bespoke manufacturing strategies for each customer advanced and fully automated assembly technologies stamping and plating
- Specialty fiber
- Complex connector and cable assemblies
- Drug and reagent handling, including cold chain
- Final assembly, packaging and labeling services, including serialization and unique device identification (UDI)
- Legal manufacturing and post-launch regulatory services
- Access to the extended Molex network of industry-leading electromechanical capabilities
- Advanced global supply chain tools and capabilities
In the last few years, Phillips Medisize and Molex, our parent company, have invested more than $500 million into our production capabilities. That’s because we are committed to continuously improving and expanding our people, our services and our ability to deliver solutions that enhance and save lives.
By the Numbers
23
Production facilities around the globe, with a dedicated NPI team in each
510K+
Sq. ft. of Class 7 & 8 clean rooms
6
MIM furnaces
6K+
Employees
2.9M+
Sq. ft. of manufacturing space
6
MAG molding machines
25+
Circuit board mfg. lines
180+
Custom assembly lines
625+
Molding machines
1,200+
Engineers, scientists and technical experts
LEARN MORE ABOUT DIFFERENT FACETS OF OUR MANUFACTURING CAPABILITIES:
Case Studies
Instilling Confidence Across Multiple Sites
Opportunity
A leading medtech company selected Phillips Medisize to manufacture components for their continuous glucose monitoring (CGM) system, and production was established at the Little Rock, Arkansas, USA, site. During visits to the site, the customer saw our wide range of capabilities, including stamping, plating and overmolding, which are essential for the sharps component of the CGM system. As a result, the customer expressed interest in expanding production in Europe.
Solution
Our diverse capabilities and successful handling of CGM products at the Little Rock site built confidence with the customer. This led them to choose Phillips Medisize to replicate the production in Poland. By being able to repeat processes and share technical knowledge across sites, Phillips Medisize exceeded customer expectations and successfully established production capabilities in Poland.
Key Takeaway
Our consistent approach to managing projects, regardless of location, instilled confidence with the customer. They were able to expect the same high level of quality and execution at both sites. Having a single global Quality Management System also significantly contributed to this project’s success.
Transitioning Plant Locations While Ensuring Compliance and Efficiency
Opportunity
A leading diagnostic company approached us with the need to scale production due to increased demand for their extraordinarily successful colon cancer screening product. Initially, they were operating with one manual line and one high-volume line at one Phillips Medisize plant location and desired a business stability plan to mitigate potential production capacity risks.
Solution
Through the trust we had developed with the customer and our ability to execute production expertly in the initial location, Phillips Medisize transitioned one of our other plant locations from a connector plant to a medical manufacturing plant. Collaboration across sites to ensure compliance and efficiency was key and was handled with extreme attention to detail while leveraging one Quality Management System that runs across all Phillips Medisize plant locations.
Key Takeaway
The above actions resulted in an increase in the customer’s manufacturing footprint while ensuring that Food and Drug Administration (FDA) medical manufacturing standards were met, along with an increase in production capacity with the ability to take a strategic approach to scaling operations while considering cost and business needs in the future.
Featured Resources
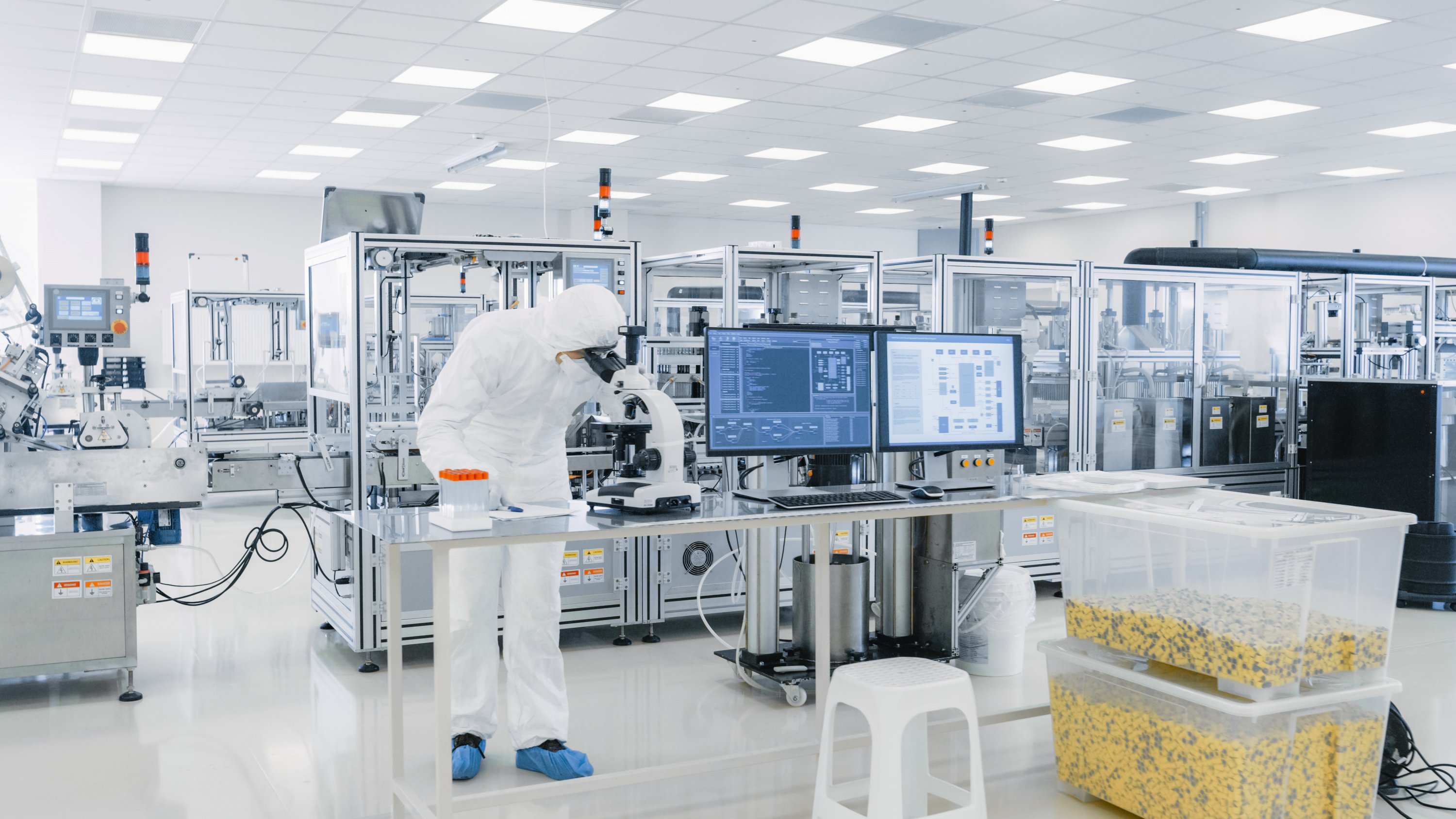
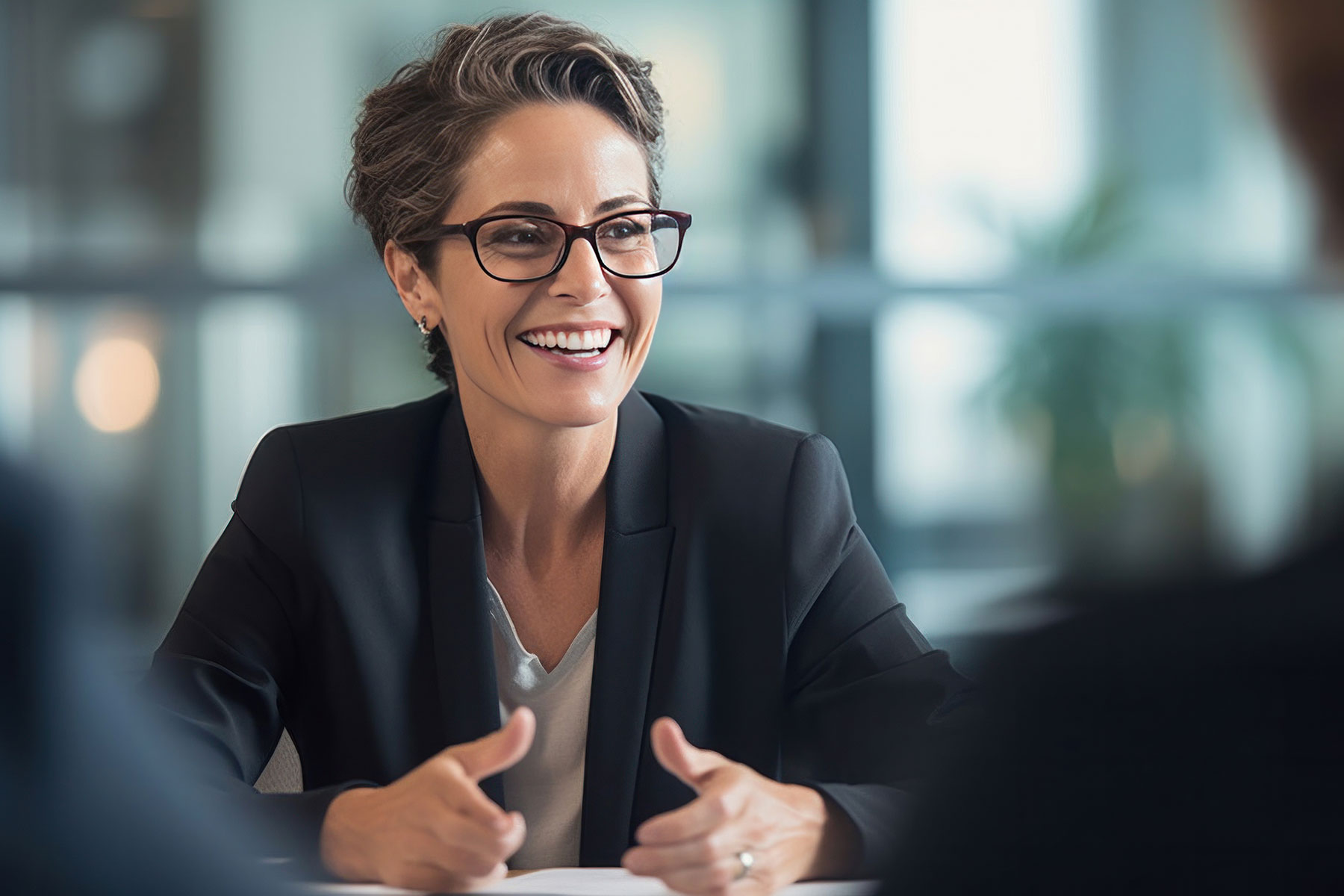
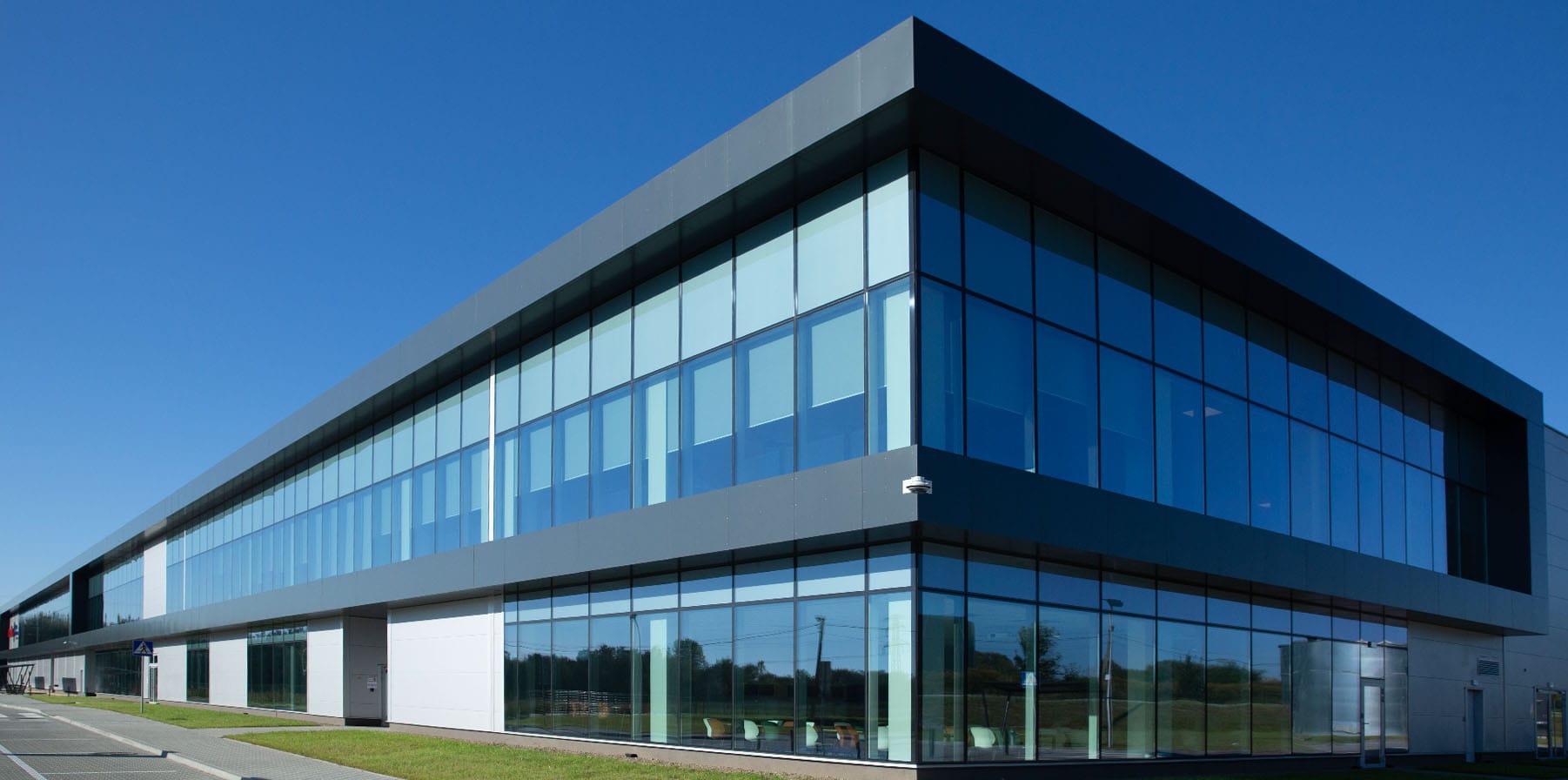