Metal injection molding (MIM) is an effective way to produce complex and precision-shaped parts from a variety of materials.
This process can commonly deliver precision end-products at costs of up to 50% less than 5-axis CNC machining—while achieving higher-resolution finishes at faster speeds than investment casting.
In addition to producing parts with complex shapes, superior strength and excellent surface finish, MIM is also valued for its high-volume manufacturing capabilities. Total cost savings generally reflect a combination of required shape, production volume, part size and material used. Given its many advantages, MIM is an increasingly popular option for key industries including medical, automotive, industrial, defense, electronics and more.
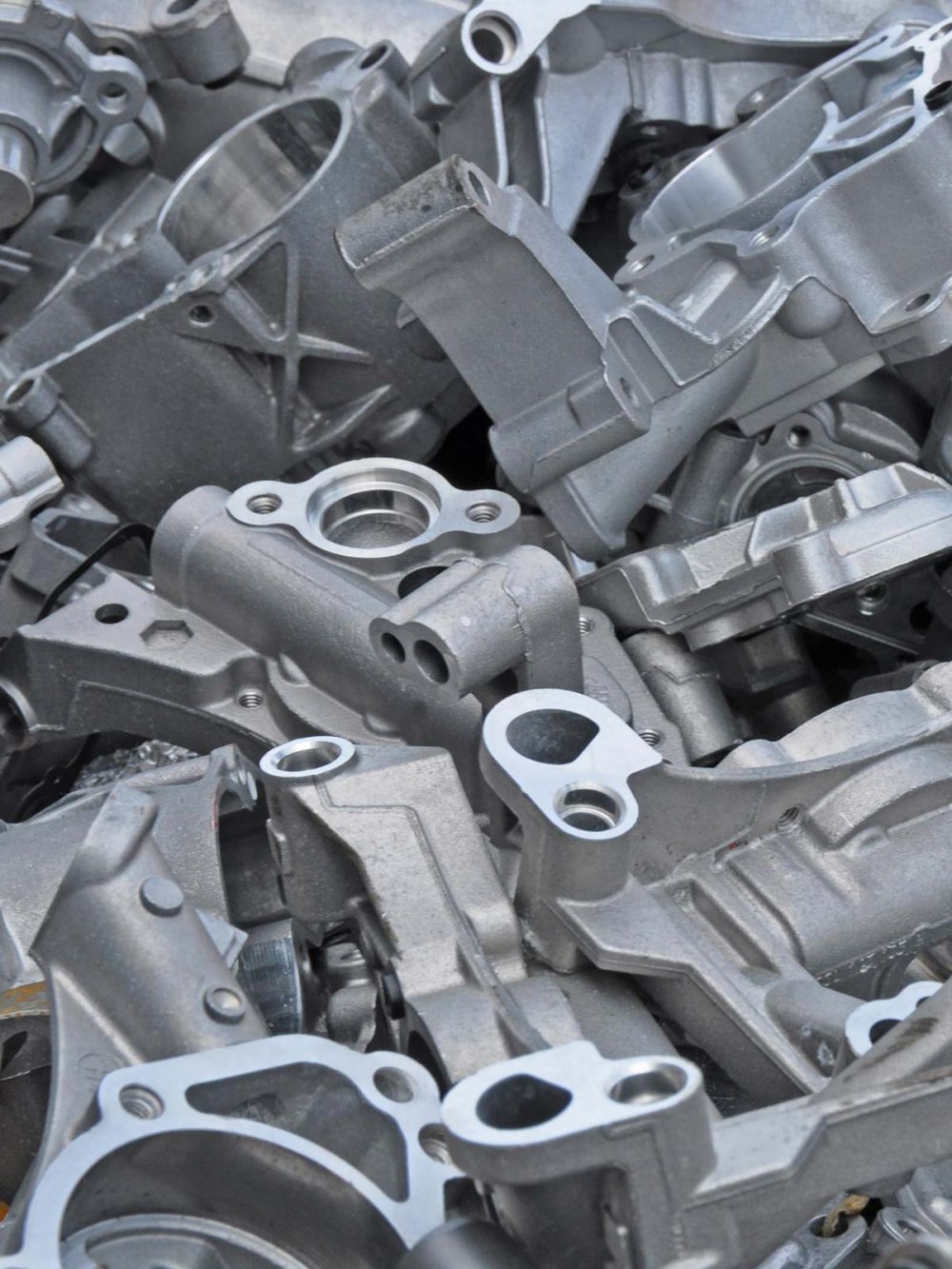
MIM is an innovative yet uniquely cost-effective injection molding method that creates precision-shaped metal parts—making it especially advantageous in situations requiring multiple secondary operations or multi-piece assembly. Because MIM accommodates numerous materials (see table below), product developers can create small custom parts and complex geometries with:
- Excellent surface finish
- 96% – 99% density
- Mechanical properties equal to wrought steel
At-a-Glance:
MIM Can Accommodate These Materials
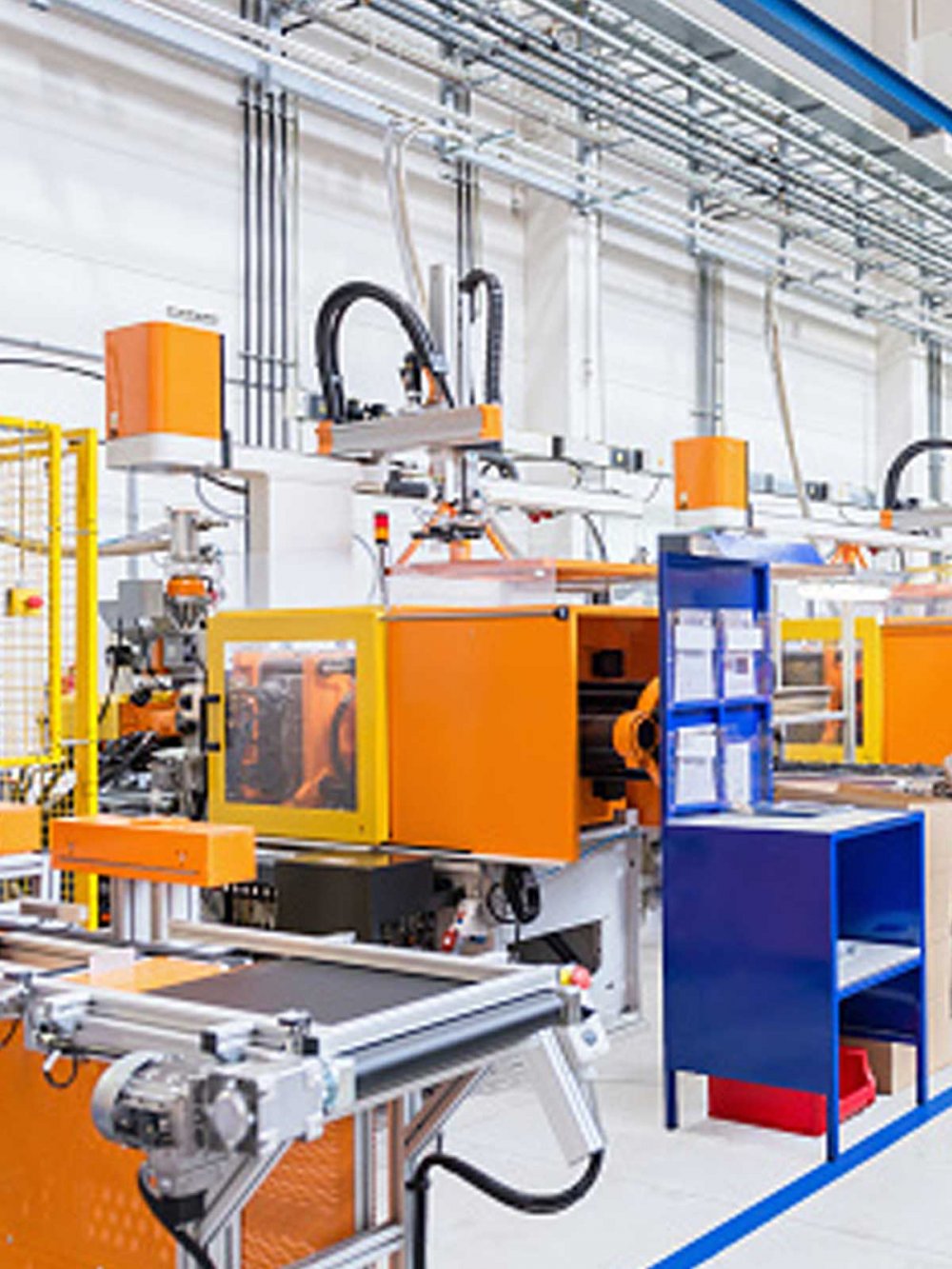
Phillips Medisize provides integrated in-house capabilities, state-of-the-art facilities and consistent communication to optimize process efficiency, control costs, tighten production timelines and reduce risk from start to finish. We help you manufacture customized metal components with a quarter-century of trusted expertise, including:
- Design assistance prior to project award
- Complete design for manufacturing (DfM) review upon project award
- Detailed customer report generation
- Gating development, venting development and moldflow analysis upon design finalization
- Optimization of critical design factors prior to mold design
Access Whitepapers, Blogs and Other Resources
Get Expert Insights
As a trusted contract design and manufacturing organization (CDMO), we can help you leverage MIM to measurably enhance your manufacturing options. Bring possibilities to life with our collaborative, one-stop support.
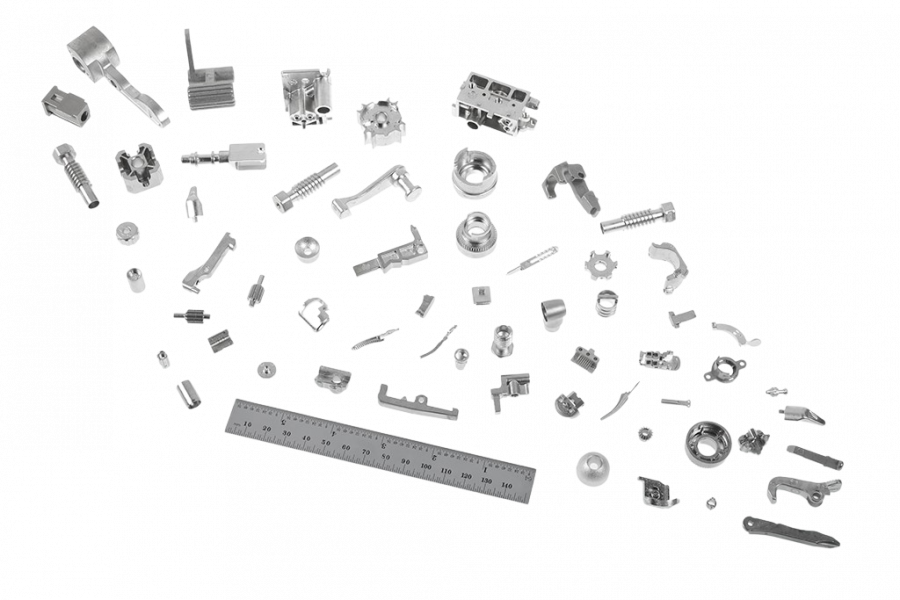
Miniaturization is a top priority for all kinds of designs—from tech gizmos to medical equipment. Electronics are often the focus of miniaturization efforts, but mechanical parts also need to shrink. This is no small challenge (pun intended). As space is…
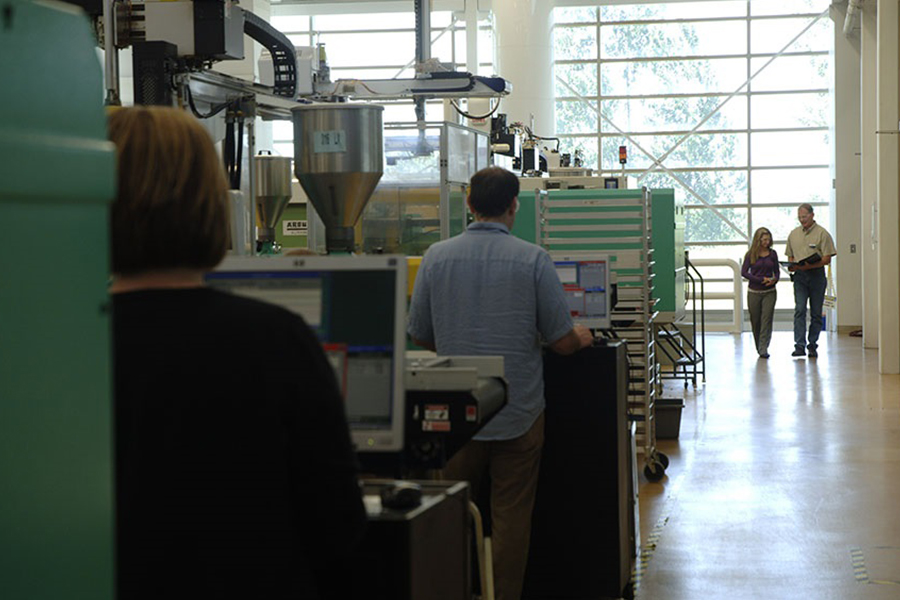
When it comes to brand reputation, quality is paramount. This is especially true when product performance is expected even under harsh conditions and in stressful situations. Standards and regulations, such as ISO 9001 and those involving ITAR and the U.S….